Filtration technology solutions for continuous processes and batch production are used extensively in the chemical, pharmaceutical, food technology, and environmental technology industries. All machinery and equipment used in these areas is characterized by its high performance and robust design. Swapping out existing interfaces for state-of-the-art visualization solutions with rapid response times can further optimize this complex equipment, thus accelerating the production process.
In this example from the chemical industry, the existing centrifuge control units were updated in order to increase the equipment’s speed. BARTEC, a specialist in safety technology, replaced the old control panel with its state-of-the-art POLARIS touch panel interface, which is designed for use in areas with an explosion hazard. Updating the centrifuge controls was sorely necessary. Centrifuges used in the chemical industry are part of a highly flexible production system, and they are continually being reconfigured for the preparation of new recipes. The old control panel’s excessively slow responses to new commands impeded the operators in their work and slowed down production. Its serial operation meant that the data import, control, keystroke processing, and image display processes were executed in a series of individual steps.
Clearly, a faster and more convenient control system was required. It could not, however, significantly alter the existing equipment, and it had to be suitable for use in hazardous areas because the materials processed in the centrifuge contain solvents. The customer was therefore looking for an option to further develop its existing equipment without involving a great deal of engineering work. BARTEC, a specialist in industrial safety technology for use in hazardous areas, had the appropriate solution. Its flexibility also enabled the Ex-area panels to be integrated into the customer’s existing equipment with no major modifications and customized to meet the customer’s requirements.
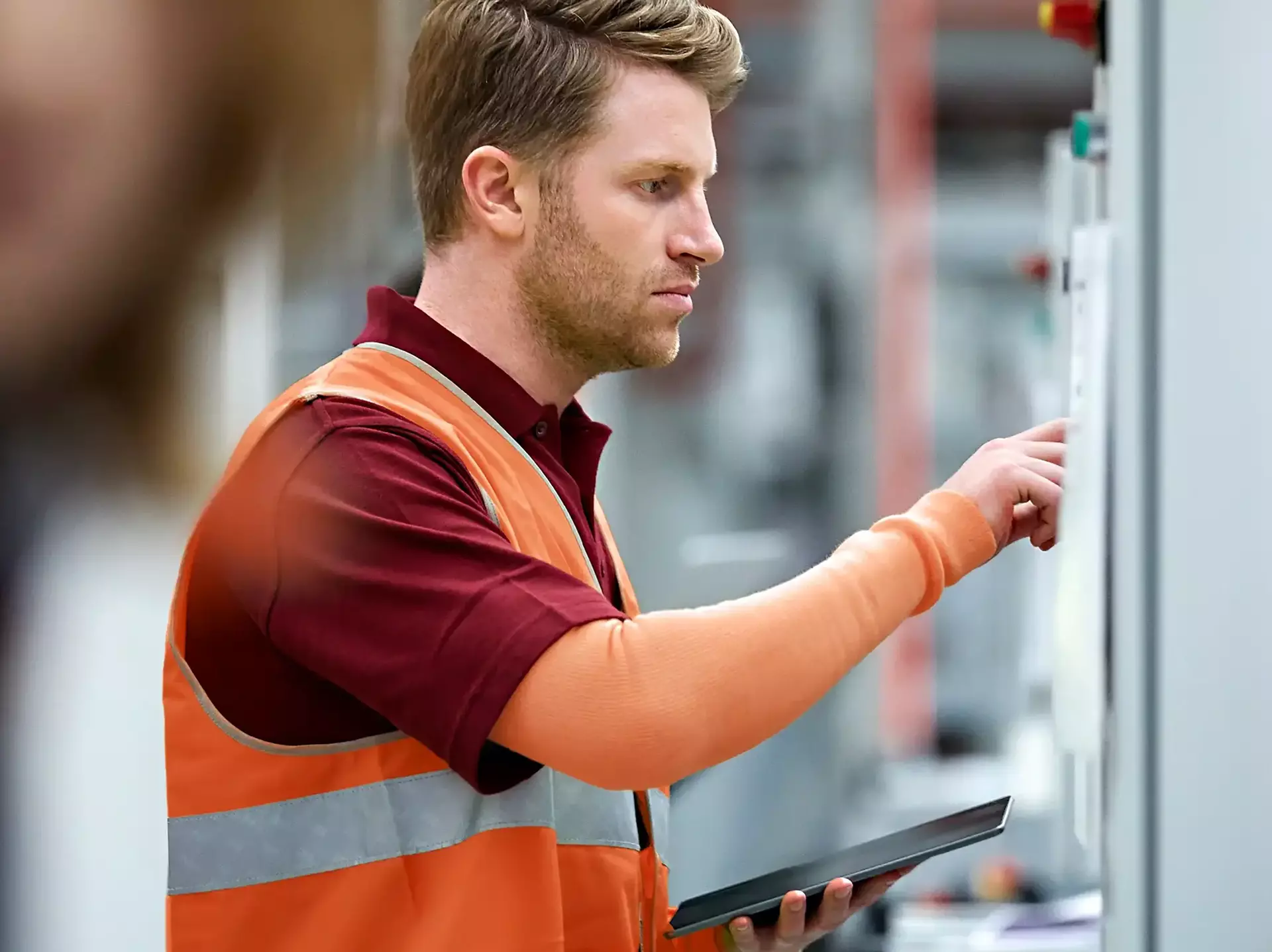
Increased productivity under Ex conditions
With the 19.1-inch POLARIS Professional Panel PC with PROFIBUS interface, communication, image display, and keystroke processing are performed in parallel. This means that all parameters are updated by the time each new log retrieval is performed. Communication processes run in the background, and new entries are immediately accepted and integrated. Comparing logs from before and after the reconfiguration showed that the previous response times of one second had become a thing of the past, placing the customer’s goal of near-real-time operations under Ex conditions within reach. This resulted in a significant increase in productivity, one which clearly demonstrates how companies can benefit from innovations without making major modifications to their systems.
A small change – with tremendous effect
All POLARIS series panels are certified according to ATEX, IECEx, InMetro, and Ghost R for worldwide use in potentially explosive gas and dust areas and are available in both standard and customized versions. The panels are equipped with an integrated Windows operating system and have both a remote desktop connection option via Ethernet and the ability to use BARTEC‘s proprietary visualization software, BMS Graf Pro 7. In this case, a decision was made in favor of BARTEC‘s proprietary solution, primarily to ensure that the customer could continue accessing previous visualization projects with minimal engineering effort. Projects could then be transferred using either the FTP Ethernet protocol or the BARTEC USB stick. The BMS Graf Pro Runtime 7 software also offers many more advantages, including integrated user administration, which allows multiple user profiles with appropriate authorizations for access and performing relevant tasks to be set up directly on the touch panel. In this way, access to individual screens, to entire process levels, or to input fields can be controlled. This considerably speeds up access for individual operators. It also virtually eradicates operator error by allowing each user to access only those areas in which they are competent, eliminating the need for time-consuming clicking through many levels. In addition to making operation safer and more reliable, the solution has also improved the process documentation. Via its operations log, BMS Graf Pro Runtime 7 delivers a report of all activities, including fillings, the beginning and end of each action, and operator entries.
Everything in view
The 19.1-inch LED displays deployed in this case were capable of processing older visualization projects, a feature that was particularly important to the customer. They did this by identifying the resolution of the project and scaling it automatically to the correct size to enable it to be viewed optimally on the screen. As a result, operators now experience convenient, easy-to-view screens with reliable touch functions.
All data is transferred to and from the control system using the BARTEC-developed PROFIBUS card. Alternative methods include serial communication via Modbus/RTU or Host Link or Ethernet-based communication via Modbus/TCP.
BARTEC experts provide companies with specific advice on updating their existing legacy solutions to leverage productivity potential – in compliance with all legal requirements, including those for hazardous areas. Consistent product updating and the further development of the BARTEC HMI portfolio form a basis for continuous new solutions, new areas of application, and increased safety and convenience.