Green hydrogen is obtained by electrolysis and this process is powered entirely by renewable energy, so it generates no polluting emissions into the atmosphere and is the cleanest and most sustainable hydrogen. Dedicating resources and fostering partnerships in hydrogen projects can therefore position companies and businesses to capitalize on the growing demand for clean energy and biofuels.
Achieving a seamless integration of hydrogen into diverse industrial sectors depends on ensuring safety and efficiency throughout the entire value chain. Hydrogen is the most abundant element in the world. It is also extremely flammable and builds enormous explosive energies with extremely hot burns and with a flame invisible to the human eye. The mix of oxygen and hydrogen have the potential to combust even with the slightest spark, a hot surface, or any other ignition source. Given its elevated hazard level, hydrogen falls into the ignition group IIC category, encompassing the most highly combustible gases. Due to these unique properties, hydrogen requires the utmost protection and safe handling. To maintain hydrogen in a controlled environment, only equipment that does not serve as an ignition source or equipment equipped with suitable ATEX measures is permissible within EX zones in the facilities and their vicinity.
Different methods of producing hydrogen have different consequences
BARTEC has 50 years of expertise in the explosion protection industry and can therefore support you throughout the whole hydrogen value chain. We offer our customers expert advice, support, and knowledge on explosion protection around the key process components. We not only offer ex-protected components and systems, but also help OEM customers to equip their solutions for hydrogen applications.
The hydrogen value chain consists of three parts: safe energy production, transport, and industrial consumption. Each of these fields requires expert know-how to ensure safety in hazardous areas, decrease costs, and guarantee compliance with regulations, codes, and standards that hydrogen requires.
Hydrogen production and conversion
Green hydrogen (GH2) is produced through electrolysis by splitting water molecules into individual elements. (2 H2O ––> 2 H2 + O2). During electrolysis, water (H2O) is split into hydrogen (H2) and oxygen (O2), which means that only hydrogen and oxygen are produced, and as we know oxygen can be safely released into the atmosphere as a by-product. Since electrolysis requires electrical energy generated through renewable energy like wind and solar power, the production of green hydrogen generates almost no greenhouse gas emissions.
In addition to electrolysis, hydrogen can also be produced by steam reforming and steam reforming of natural gas of biomethane and pyrolysis of biogenic feedstocks (CH4 + H2O ––> 3 H2 + CO), but green hydrogen is the cleanest way to produce hydrogen with the lowest possible (close to zero) CO2 emissions.
But why choose BARTEC? Because we have already successfully helped electrolyzer OEMs to design ex-protected units. Our components are part of the world’s biggest ever-realized Hydrogen Production site.
Maintaining purity and dryness is crucial for operational integrity and safety. Excess moisture can lead to corrosion, erosion, and safety hazards in hydrogen production. To ensure compliance with moisture limits, reliable moisture analyzers are indispensable. BARTEC’s solution HYGROPHIL F trace moisture analyzers offer robustness and accuracy, enabling precise measurements even in dynamic production environments. It is a high-quality, fibre-optic hygrometer for measuring the moisture or trace humidity at low dew-point temperatures in gases and liquids. With features like independent calibration verification and easy maintenance, these sensors streamline operations without compromising safety. Investing in such solutions isn't just regulatory compliance — it's a commitment to operational excellence and safety assurance.
Hydrogen storage and transportation
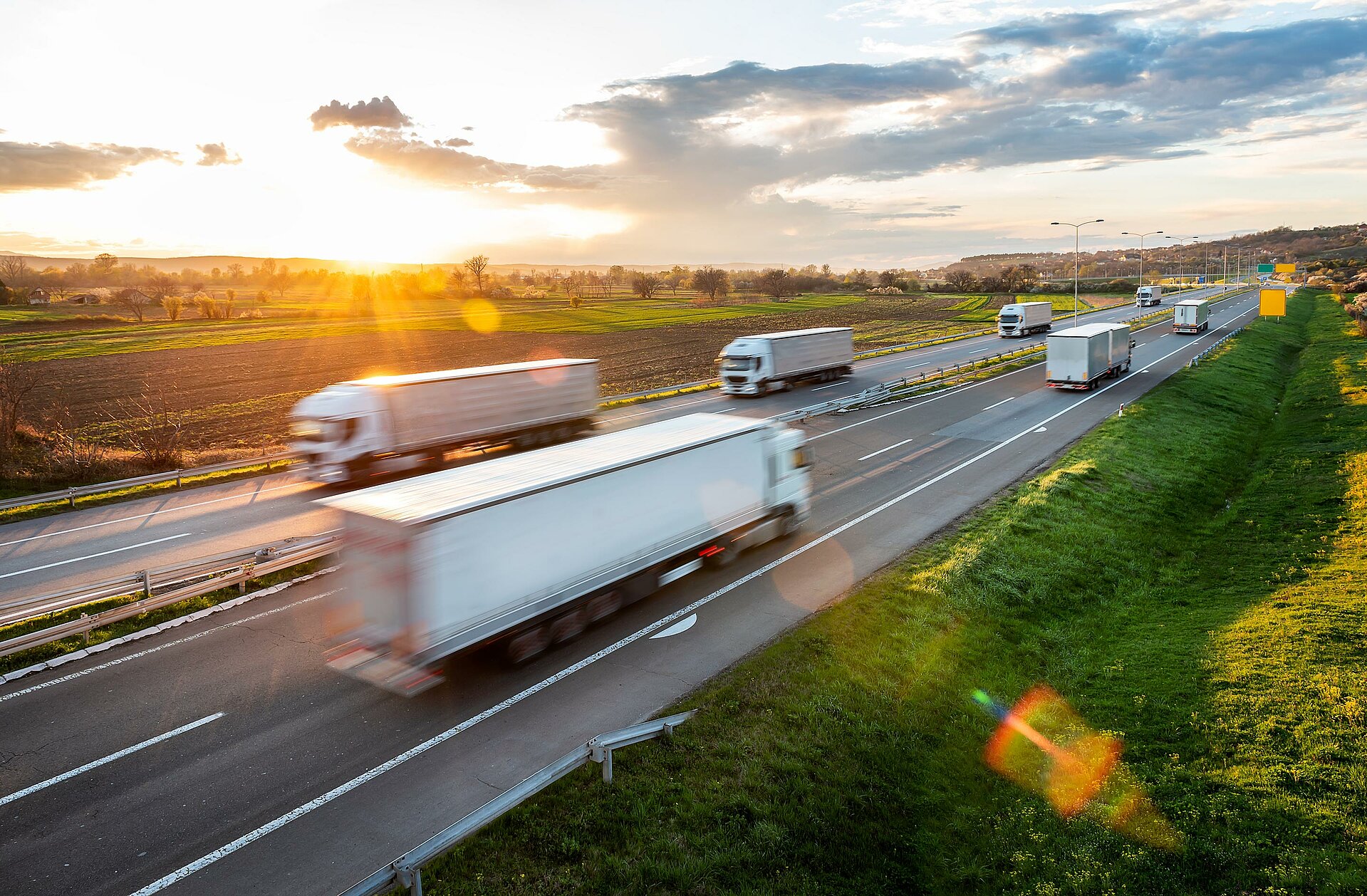
After hydrogen is produced and processed, the next step is the need for its safe storage and distribution. Under standard conditions, at room temperature and room pressure, hydrogen is colorless, odorless, tasteless, and non-toxic gas. Despite being non-toxic, hydrogen is highly flammable and can combust in the presence of oxygen, forming water vapor as a byproduct.
Since hydrogen can be stored in either its gaseous or liquid state, there are several hydrogen storage methods. It's important to note that hydrogen's boiling point is extremely low at -252.9°C (-423.2°F). This means that liquid hydrogen requires extremely low temperatures for safe storage or needs to be bonded organically, as seen in solutions like Liquid Organic Hydrogen Carriers (LOHC). On the other hand, gaseous hydrogen, when stored at regular temperatures, necessitates high-pressure solutions for both storage and transport to increase energy density and thus transport capacity.
It's important to consider that the current infrastructure designed for the transmission and distribution of natural gas can, in theory, be repurposed for hydrogen use. However, there are several limitations and specific measures that need to be implemented to ensure compatibility and safety.
In BARTEC we differentiate our solutions for use in larger systems for hydrogen storage and transportation and solutions for smaller on-site infrastructure or small-volume transportation. Large-scale transmission of hydrogen can be possible via pipelines for connection to tank stations for ships as well as for road transportation. Small-scale transmission of hydrogen can take place through road trailers either for intercompany or custody transfer delivering to storage facilities at filling stations or as swappable trailers on site.
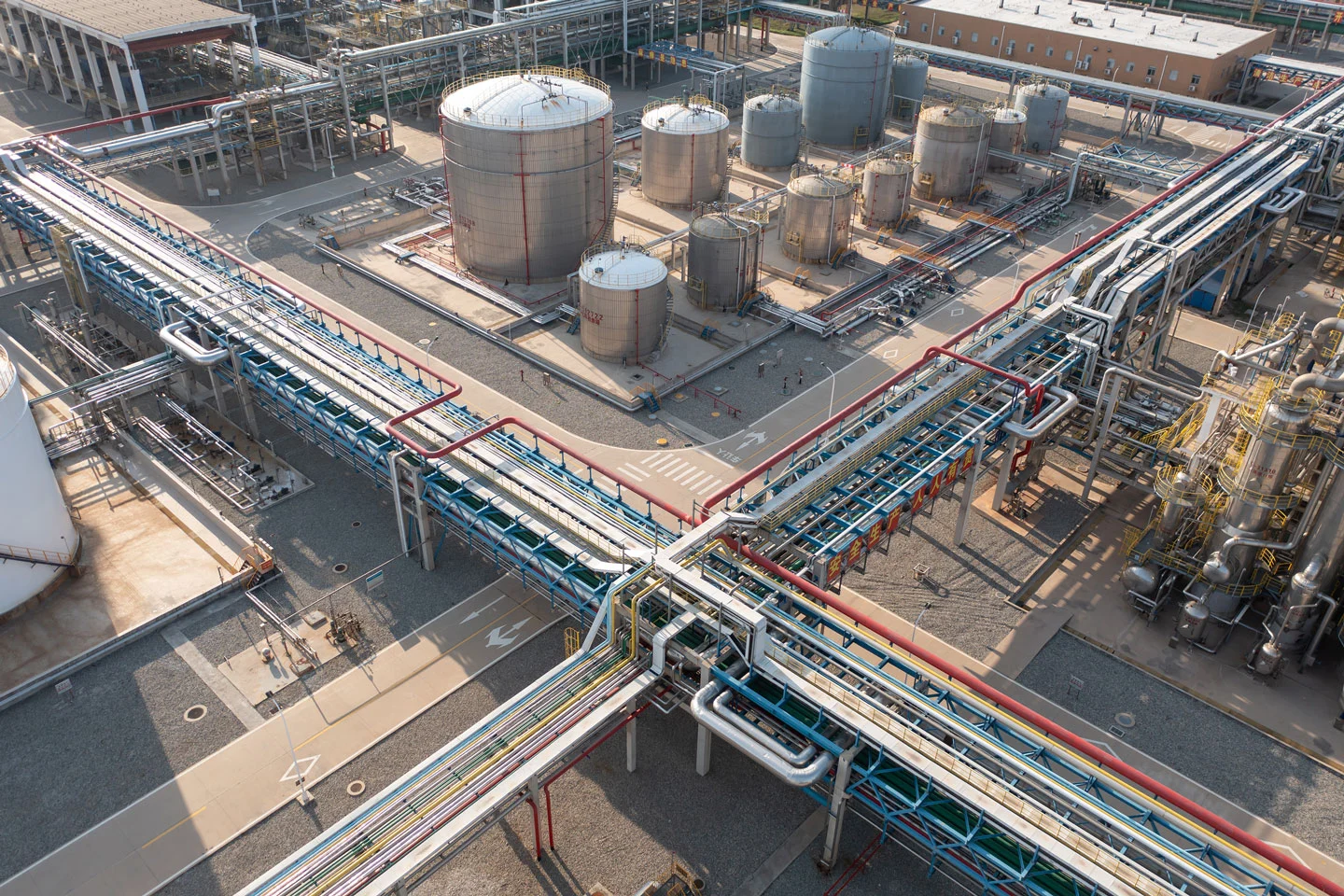
One notable benefit of hydrogen is its capacity for prolonged storage with minimal losses in its gaseous state. However, it's important to note that hydrogen exhibits a lower volumetric energy density at atmospheric pressure when compared to alternative energy carriers like natural gas or oil. While this characteristic is less problematic in stationary settings where larger storage tanks with lower pressure are acceptable, it becomes a notable concern in mobile applications where the size and weight of tanks become significant considerations.
For all these applications BARTEC provides specific explosion-protected electrotechnical solutions like lighting, control and connection equipment, and visualization, whereas for the small-scale transportation BARTEC also delivers monitoring, controlling and measuring technology with back-office communication.
BARTEC offers ultra-modern technology that combines four main functions into one single system: measuring, monitoring, controlling and data transfering for tank trucks that transport hazardous gases and liquids. BARTEC’s H2 Trailer-Swap Logistics Solution ensures a safe and efficient hydrogen distribution. From calibrated measurements to leakage detection and continuous fill level monitoring, all critical functionalities are included. Moreover, it includes the Track & Trace software for data visualization and evaluation, coupled with automated data transmission. This hydrogen system's ultimate goal is to guarantee safe trailer handling and optimize hydrogen trailer (swap) logistics. In combination with an integrated billing system, it leads to a highly efficient transport of hydrogen in compressed gaseous and liquified form. Maximum attention is paid to safe loading and delivery, as well as the simplicity of calibrating the system without the dismounting of the meter section. Automated Data Transfer automatically ensures two-way communication between hydrogen MEGC/trailer and office.
Hydrogen can be delivered to its intended destination using either high-pressure containers, liquid hydrogen vessels or pipelines. The challenges encountered in storing and distributing hydrogen in high-pressure tanks mirror those faced in managing high-pressure vessels. Transportation of hydrogen in high-pressure tanks can be achieved through road, rail, or maritime means, providing flexibility and the ability to reach diverse locations without the need for extensive new infrastructure.
For the distribution of large quantities of hydrogen, transmission through pipelines is the most practical option. Gas pipelines offer a cost-effective method for transporting significant energy volumes, surpassing the efficiency of electricity transmission via overhead power lines. In certain countries, existing gas pipeline infrastructure can be repurposed for hydrogen transport with relatively small custom modifications.
To ensure safe and continuous operation throughout the years it is recommended to protect all pipelines from frost and condensation via trace heating solutions.
Although on-site storage and distribution of hydrogen are achievable, they require the establishment of a clear safety plan and thorough testing before implementation. The primary obstacles involve the utilization of high-pressure tanks and the intricate design and operation of the filling station. Additionally, companies must guarantee the integrity of components and offer appropriate training to employees to ensure the secure handling of hydrogen.
Hydrogen Applications
In (new) energy and material applications, operators and component manufacturers need to be aware of the risks associated with high-pressure devices, the safe handling of hydrogen, and the conformity of parts, devices, and systems. For mobility applications, approval, global market access, and testing of components for hydrogen are crucial.
BARTEC’s product portfolio is ready to serve both the already existing “new energy” applications as well as all new or specific upscaled hydrogen applications. BARTEC provides specific explosion-protected solutions fully customizable thanks to our in-house engineering capabilities and decades of experience in international projects. We deliver a full range of electrical safety systems and components which mainly include:
Operating & monitoring systems and automation interfaces for controlling and protecting your assets thanks to our reliable HMI and Bus systems. Our POLARIS HMI series is the best-in-class solution for all tasks related to process visualization as well as operation and monitoring, while our MODEX remote I/O allows a safe and reliable connection of standard bus systems in hazardous areas. Both grant the necessary data transmission, power and signal for achieving the highest level of safety and efficiency.
Electrical enclosures, systems and components with different types of protection ensure the right level of safety for any plants need. Consisting of a wide range of components and solutions of many standard sizes and materials, they are suitable for any application where a potentially explosive atmosphere may be present. They include control and monitoring devices, safety switches, Ex d and Ex e enclosures and panels, for granting efficiency and reliability wherever you need. We also provide control cabinets with remote I/O systems for any hydrogen applications, including the electrolyzer one.
Thanks to decades of experience in the field of hazardous areas, we have the right knowledge and know-how to provide the best solution to protect safe-area industrial components and make them suitable for any hydrogen applications.
Turnkey trace heating solutions for frost protection of pipes and vessels, as well as fundament heating for LOHC tanks. Our series resistance trace heaters are simple and flexible to install, providing constant heating regardless of surrounding temperatures. Self-regulating heat tracers can be cut to length and are energy efficient as they power down with rising temperature, also ensuring safety in the hazard area.
IIoT & Connectivity solutions from BARTEC are the broadest range at world allowing you to extend your network into hazardous areas. They include antennas, wireless IIoT sensors and networks for fast and safe data flow processes as well as workers and assets tracking systems. Our solutions make it easy to implement wireless networks in hazardous areas: they can be used for all types of Wi-Fi, BLE, 4G/5G access points, radios, gateways and repeaters with internal and/or external antennas.
Lighting solutions which, thanks to our state-of-the-art LED technology, improve the plant performance and the wellbeing of workers providing a better visibility, even in critical conditions. Our wide range of excellent lighting fixtures with different shapes and materials are suitable for hazardous areas and safe area industry ensuring energy and cost savings as well as great reliability and easy maintenance.
Support Services: Assistance with measuring, monitoring, controlling, and data transferring for hydrogen storage and transportation.
All our solutions are certified according to the most important international certifications, that’s why they always represent the best answer for any application’s needs worldwide.
In conclusion, as the explosion protection industry embraces the potential of hydrogen, careful consideration of safety measures, technological advancements, and collaborative efforts will be key to unlocking its full benefits. By navigating these challenges with diligence and innovation, we at BARTEC pave the way for a safer, more sustainable future where hydrogen plays a pivotal role in shaping the landscape of explosion protection.